You Kneed to Know…
- Amy McDougall
- Oct 21, 2024
- 2 min read
By: Amy McDougall
When it comes to knee replacement surgery, ensuring the highest quality of materials used in the implant is paramount. One crucial material is titanium, known for its strength, lightweight properties, and biocompatibility (American Academy of Orthopaedic Surgeons). Recent investigations into the aerospace industry reveal significant issues with titanium used in aircraft, raising important questions about material provenance and quality control. Why would this matter to me? Being a United One Million Miler and being destined for a knee replacement from too much tennis, I worry about this.
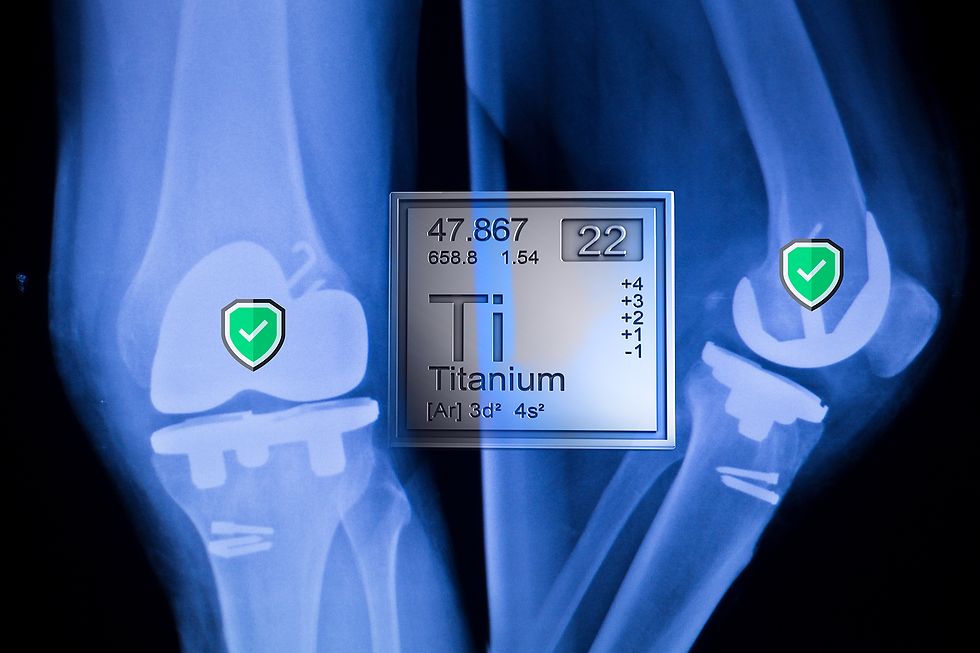
The Federal Aviation Administration (FAA) and European safety regulators are currently investigating the use of titanium with falsified documentation in Boeing and Airbus planes (North State Journal). These parts were supplied by a Chinese manufacturer, and while Boeing and Airbus have removed suspect parts from undelivered aircraft, the investigation is ongoing to assess the full extent of the issue (Reuters, 2024). Over 1,000 tests were conducted to verify the affected material's properties, highlighting the seriousness of the situation. This underscores the need for improved methods to ensure the authenticity and quality of critical supply chain materials.
The aerospace industry’s experience illustrates a broader concern about the presence of counterfeit or improperly documented parts in crucial supply chains. Aircraft manufacturers depend on a complex network of suppliers, which makes oversight and quality control challenging (Aerospace Manufacturing and Design). The industry has responded by forming task forces to address these issues, yet traceability and verification remain significant challenges.
These challenges in the aerospace sector highlight the importance of material integrity and verification across all critical applications, including medical implants. While the medical devices industry has rigorous standards for material quality, the incidents in aerospace raise thought-provoking questions about how materials are sourced and verified. If issues of documentation and authenticity can affect the aerospace industry, it’s crucial for all sectors to remain vigilant.
The shift towards Chinese titanium suppliers due to increased demand and supply constraints from traditional sources adds another layer of complexity (Aerospace Industry Reports). Chinese sources often have opaque supply chains, making it difficult to ensure the purity and quality of the metal. This situation emphasizes the need for enhanced traceability and quality control measures to prevent contamination and ensure material performance.
For knee replacements, using high-quality titanium is vital to avoid complications such as implant rejection, infection, or mechanical failure (Journal of Orthopaedic Surgery). Patients should be proactive in seeking information about the origin and quality of titanium used in their implants. Ensuring that titanium is sourced from reputable suppliers and meets all necessary medical standards is essential for long-term success and safety.
The aerospace industry’s current challenges with titanium serve as a reminder of the critical importance of material quality and traceability in all applications. As patients prepare for knee replacement surgery, they should demand transparency and proof of material quality to safeguard their health and well-being. Transparency and accountability are crucial in ensuring that companies meet their claims and maintain the highest standards. Whether in aerospace or medical devices, the call for improved verification and quality control is clear.
Comments